一、引言
在工業領域不斷革新的當下,工業 4.0 概念引發全球制造業變革。電加熱硫化罐作為橡膠等行業的關鍵設備,其智能化改造與工業 4.0 的結合成為提升生產效率、產品質量以及企業競爭力的重要路徑。
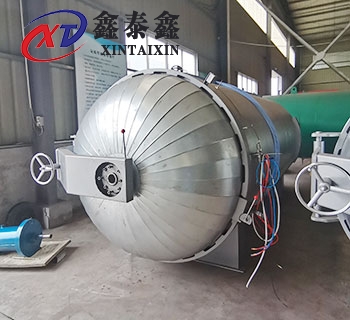
二、電加熱硫化罐智能化改造的必要性
傳統電加熱硫化罐的弊端:傳統電加熱硫化罐依賴人工操作,硫化過程中溫度、壓力控制精度欠佳,導致產品質量穩定性差。例如在橡膠制品硫化時,溫度波動可能使橡膠硬度、彈性等物理性能出現偏差。人工巡檢記錄數據,不僅耗費人力,而且數據記錄存在滯后性和誤差,難以實時反映電加熱硫化罐運行狀態。
智能化改造的迫切性:市場對橡膠等硫化產品質量和生產效率要求不斷提高,傳統電加熱硫化罐已無法滿足需求。通過智能化改造,可實現硫化過程自動化、精準化控制,契合現代工業生產模式,提升企業在市場中的適應能力和競爭力。
三、電加熱硫化罐智能化改造與工業 4.0 的結合點設備互聯互通:運用工業以太網、物聯網等技術,將電加熱硫化罐與工廠內其他設備(如原材料輸送設備、成品檢測設備等)連接成網。每個電加熱硫化罐配備傳感器和智能終端,實時采集溫度、壓力、運行時間等數據,并上傳至工廠數據中心,實現設備之間數據共享與協同工作。例如,硫化完成后,系統自動將產品信息傳輸至檢測設備,啟動檢測流程。
自動化控制與優化:引入先進的自動化控制系統,替代人工手動調節硫化參數。根據不同產品硫化工藝要求,在系統中預設參數,系統依據實時監測數據自動調整溫度、壓力等,確保硫化過程精準無誤。利用大數據分析和機器學習算法,對歷史生產數據進行挖掘,優化硫化工藝參數,提升產品質量和生產效率。例如,通過分析不同批次產品質量數據和對應硫化參數,找出最佳參數組合,用于后續生產。
生產過程可視化:借助工業軟件和監控平臺,構建電加熱硫化罐生產過程可視化界面。操作人員可在監控中心實時查看每個電加熱硫化罐運行狀態、參數變化曲線等信息,對生產過程一目了然。當出現異常情況(如溫度過高、壓力過低)時,系統自動報警并顯示故障位置和原因,方便操作人員及時處理,保障生產安全穩定運行。
智能維護與預測性保養:在電加熱硫化罐關鍵部件安裝振動、溫度、磨損等傳感器,實時監測設備運行狀態。通過數據分析預測設備故障發生概率,提前安排維護保養,避免設備突發故障導致生產中斷。例如,當監測到某部件磨損接近閾值時,系統發出預警,提醒維修人員及時更換部件,降低設備維護成本和生產損失。
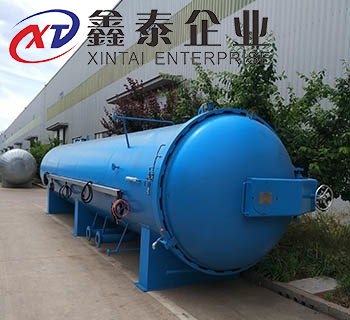
四、電加熱硫化罐智能化改造的實施步驟
需求分析與方案設計:深入了解企業生產現狀、產品工藝要求以及未來發展規劃,對電加熱硫化罐智能化改造需求進行全面梳理。根據需求制定詳細改造方案,包括選用的智能化技術、設備選型、系統架構設計以及實施計劃等。
設備升級與系統集成:按照方案對電加熱硫化罐進行硬件升級,安裝傳感器、智能控制器、通信模塊等設備。同時,將這些設備與工廠原有自動化系統、信息化管理系統進行集成,確保數據傳輸順暢和系統協同工作。
軟件開發與調試:開發電加熱硫化罐智能化控制系統軟件,實現參數設定、自動化控制、數據采集與分析、可視化監控等功能。在軟件調試過程中,模擬各種生產場景,對系統穩定性、準確性和可靠性進行測試優化,確保軟件滿足生產需求。
人員培訓與上線運行:對企業操作人員、技術人員進行智能化系統操作和維護培訓,使其熟悉新系統功能和操作流程,掌握常見故障處理方法。在培訓完成后,將智能化改造后的電加熱硫化罐正式投入生產運行,并持續跟蹤運行情況,及時解決出現的問題。
五、電加熱硫化罐智能化改造與工業 4.0 結合的效益提高生產效率:自動化控制減少人工干預,縮短硫化周期,提升單位時間內產品產量。例如,原本一批橡膠制品硫化需要 8 小時,智能化改造后可縮短至 6 小時,生產效率大幅提高。
提升產品質量:精準的溫度、壓力控制確保硫化過程一致性,產品質量穩定性顯著提升,次品率降低。如橡膠產品次品率從原來的 5% 降低至 1%,提高了產品市場競爭力。
降低生產成本:智能維護減少設備故障停機時間和維修成本;自動化操作減少人工需求,降低人力成本。例如,每年設備維修成本降低 30%,人力成本降低 20%。
增強企業競爭力:智能化改造使企業生產模式更加先進高效,能夠快速響應市場變化,開發新產品,拓展市場份額,在激烈的市場競爭中占據優勢地位。
六、結論
電加熱硫化罐智能化改造與工業 4.0 的結合,是橡膠等行業實現轉型升級的關鍵舉措。通過設備互聯互通、自動化控制、生產過程可視化以及智能維護等方面的改造,企業能夠獲得生產效率提升、產品質量優化、成本降低等多重效益,為企業可持續發展注入強大動力,在未來工業發展浪潮中贏得先機。